Benefits of True Cloud ERP for Discrete and Batch Manufacturing
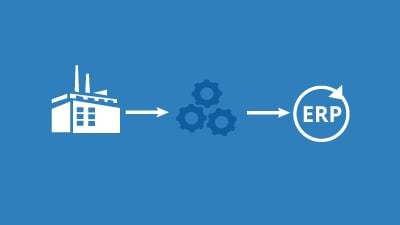
ERP solutions are innovating businesses across every industry and sector — manufacturing is certainly one of those that is seeing more and more businesses implementing this modern technology that will improve internal procedures for increased efficiency and drive business growth.
Flexible business processes help to plan and control manufacturing operations; regardless of whether the overall focus of the manufacturing model is discrete or batch. Let’s look at each of these and how and ERP can help entities improve operations.
Discrete Manufacturing
This form of manufacturing involves building individual units for shipment. Manufacturers that use the discrete process develop individual items that represent a particular product line — items can be easily touched, seen, and even counted.
Products that are created through this manufacturing process can include nuts and bolts, brackets, wires, assemblies, and other products. Larger items that are made from discrete manufacturing include automobiles, furniture, airplanes, toys, smartphones, and defense systems.
These products have one unique quality; they can be broken down when the lifecycle has expired and the basic components can be recycled or otherwise disposed of.
What makes a process discrete:
- Products are compiled of parts that can be sourced, etc.
- Parts can be disassembled and disposed of or recycled at the end of the product lifecycle
- Utilizes a bill of materials (BOM)
- Assembles in a linear or routing way
- Examples include automobiles, computers, etc.
A cloud-based ERP system offers visibility that allows companies to better control its processes and ultimately eliminate waste, while reducing the time allotted for production. The solution provides the basic functions of an ERP that is designed for manufacturing. The specific manufacturer can then further integrate systems for a more customized approach.
Batch Manufacturing
Products are made as specific groups or with set amounts, all within a frame of time with this form of manufacturing. A batch may go through a series of steps to reach the desired result in more complicated and sizeable manufacturing processes. Layouts in batch manufacturing are typically done by function: a weld shop, a paint shop, a fabrication shop, etc.
Also known as “batch and queue,” products are produced and shipped to the next stage, often sitting in line awaiting attention at a progressive level. This method combines supplies, ingredients or raw substances using a formula or recipe. Examples of items created through this process include: food, beverages, refined oil, gasoline, pharmaceuticals, chemicals, and plastics. There are also core products such as wheat, corn, and coffee that are crafted through batch manufacturing.
Volumes of raw materials are refined and processed for sale, while there are no discrete units of production. Through batch manufacturing, a product is fully produced and packaged for shipment.
What makes a process batch:
- Products that are created using a formula to refine materials
- Products cannot be broken down into constituent parts
- Uses a formula or recipe
- Blends in a batch
- Examples are drugs or food products
Because components are combined in the manufacturing process, they cannot be returned to an original state. When changes need to be made, those must happen systematically with companies keeping a limber approach and modifying recipes readily as needed. Perhaps one client prefers a product that is sweeter than another client, or gasoline for commercial vehicles will greatly differ than that used for jetliners. An agile ERP system can help keep track of these matters, providing a smooth and cost-effective process for the business.
Discrete vs. Batch Manufacturing
These processes are not like one another — they have differing structures and needs — and the software architectures used by manufacturing companies should reflect the individual requirements, taking into account the products that are produced and the materials that are used.
Batch manufacturing can bring with it complexities, as there is greater risk to employees managing the process, as well as consumers who are purchasing and buying finished products. An ERP solution that can help plant managers to monitor and track complex and specialized processes is key.
Considerations are safety laws and regulations, consumer demand for healthier and more environmentally-friendly products, as well as day-to-day functions such as operational planning — which can be intricate and demand careful handling — of product recipes, accounting, customer management, sales, and purchasing. The ability to weigh product volumes or govern the containerization of bulk goods, can prove beneficial to companies dealing with batch manufacturing.
Companies focused on discrete manufacturing should implement a system that offers robust parts tracking and assembly monitoring; lifecycle management and process mapping are also an area of focus for these manufacturers.
Features such as barcode scanning and RFID (radio-frequency identification) tracking can be utilized with both processes, but will be much more useful for discrete manufacturing, where individual parts move through the assembly process.
Learn more in Top 9 Manufacturing ERP Software Modules.
Getting Started
A modern ERP solution can benefit both discrete and batch manufacturers. Acumatica for Cloud Manufacturing ERP Software offer the fastest-growing, award-winning solution and is designed specifically to perform manufacturing management applications.
Partnering for success is paramount for any organization looking to improve efficiencies and growth. At Cloud 9 ERP Solutions, we have a proven track record that business leaders can count on. Read our testimonials, and contact us to learn more!
Interested in learning more? Watch our Acumatica Manufacturing demo or read our article Why Manufacturing Companies Need an Industry-Specific ERP Solution.