Inventory Replenishment Methods: Everything You Need to Know
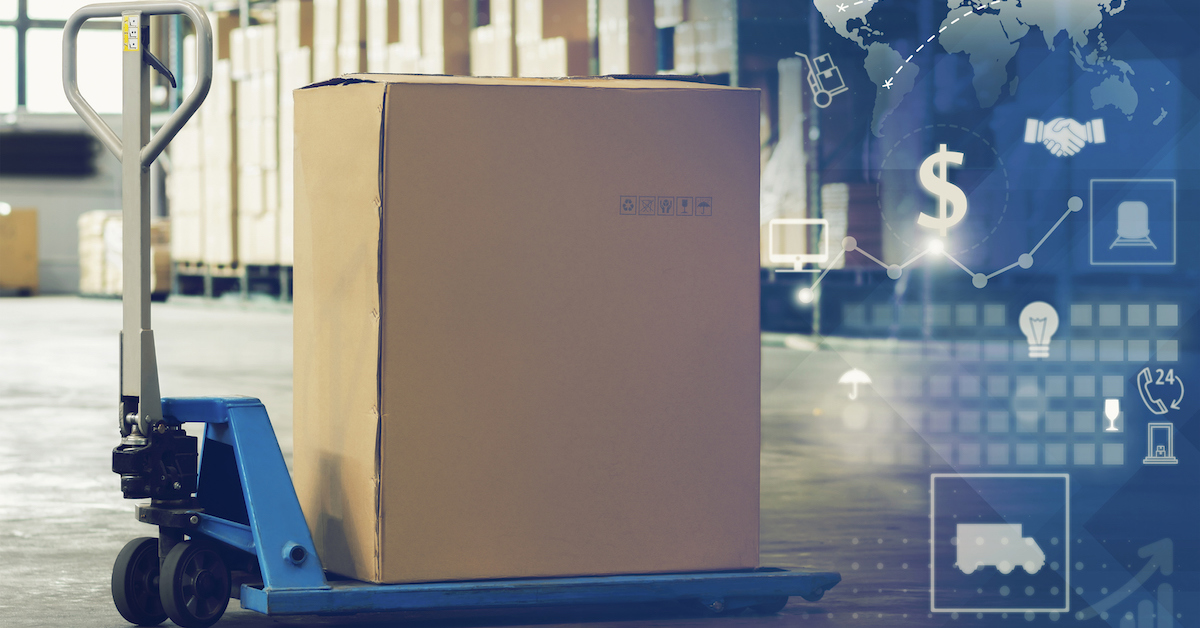
As a distribution company, you might be feeling overwhelmed with the amount of inventory you have or how to organize and replace it. Having a strong and efficient inventory replenishment method can help you streamline your business processes to meet the high demands you are facing from your customers. In this article, we’ll go through the basics of inventory replenishment and how having it can help you as a business owner.
So, What are Inventory Replenishment Methods, Anyway?
Simply put, inventory replenishment management defines the process when the products that are held in regular inventory are moved to more transitionary locations such as shipping inventory; it’s also the organizational system. Inventory replenishment is what keeps the things you sell moving. If your products are in high demand, you’ll need a way to effectively replenish them. There are different ways you can replenish your inventory, but finding the one the works best for your business is key to ensuring that your operation is running smoothly.
Benefits of Inventory Replenishment Systems
If you haven’t utilized an inventory replenishment service before, you probably don’t know all the benefits that can come with it.
Minimizing Admin Tasks
First, it can optimize your backend procedures by lessening the amount of time you are focusing on administrative tasks. An automated system that is able to give you flexibility and control over how you identify and track your items can mean you are able to focus more of your time on other things, increasing the efficiency of your organization. . It also cuts out costs to hire someone like a virtual assistant who would be taking care of more administrative tasks that you didn’t have time for.
Identifying Areas of Improvement
It can also help you to identify areas for improvement such as where inventory isn’t moving as quickly as you’d like.
Meeting the Demands of Your Customers
Overall, however, having an inventory replenishment system can help you meet the demands of customers that you might otherwise not be able to meet.
Organizing Your Inventory Replenishment System
There are many ways that you can work to replenish your inventory, including by:
- Cost
- Number of products available
- Date in which they arrived at your facility
Basically, anything that can identify a product from another one is a way you can organize it with an inventory management system.
What You Should Know Before Selecting an Inventory Replenishment System
Before selecting a system, you should be aware of all your operating procedures and have an accurate definition of how you are currently tracking your inventory. You should also perform a quality analysis of your current inventory management and replenishment system. Ask yourself these questions:
- What areas are you struggling in?
- Have you had demands on certain products that you aren’t able to fill?
- Are you selling out quickly of a specific item or have too many laying around in your back storage?
If you are noticing significant problems in any areas of your business, let these issues guide you in finding a system that will best fit your needs rather than basing it off of the strengths of your organization.
An example of an outstanding inventory management and replenishment system is the Acumatica Inventory Management software. This system covers all the basics plus more of what you’ll need for an outstanding inventory management system:
- Differing valuation methods
- Multiple warehouses
- Serial numbering
- Location control
- Able to subitem inventory
- Assign expiration date
- Inventory accounts
- Physical inventory
- Audit trail
As you can see, the program itself is versatile and can adapt to different types of businesses. It’s extremely useful for businesses that offer more than one product or service.
Get Started Today
Cloud 9 ERP Solutions, a Gold-Certified Acumatica Partner, can help you control system-wide inventory across geographically-dispersed locations to efficiently manage your distribution process without losing track sight of costs. Receive inventory to a specific location and drill down to change item default lot/serial numbers, valuation methods, accounts, and more. Manage perishable inventory, automate replenishment, and build or disassemble kits.
Take a deep into Acumatica's inventory replenishment features in our video below:
For more information on the Acumatica Inventory Management software, contact us today! Here at Cloud 9 ERP Solutions, we can help you make the most of Acumatica’s software and, in turn, use replenishment and automation to increase inventory turns.
Additional Distribution Resources
How to Optimize Inventory, Reduce Costs, and Automate Your Supply Chain
Six Features to Look for in a Modern Warehouse Management and Distribution ERP
Pivoting Toward Recovery: Combining Inventory Optimization and AP